Czy 10 minut na produkcji to dużo?
Czy wiesz, że te pozornie krótkie 10 minut może zadecydować o sukcesie lub porażce całego dnia produkcyjnego? Zatrzymania, opóźnienia, nieefektywne procesy – każda minuta ma znaczenie. Ale czy naprawdę zdajemy sobie sprawę, jak wielką różnicę może zrobić tak krótki czas?
Przekonaj się, dlaczego każda minuta w produkcji ma swoją wagę, i dowiedz się, jak optymalizować procesy, by nigdy nie zmarnować ani sekundy.
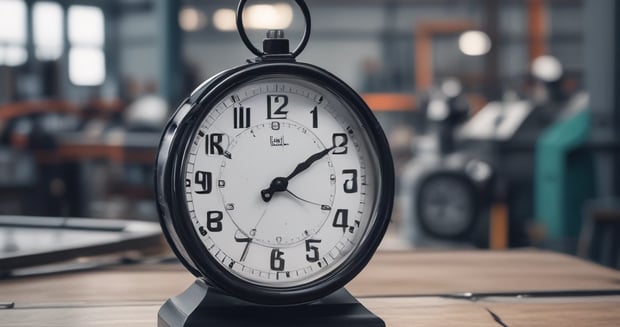
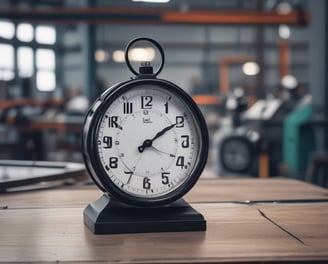
W świecie produkcji każda minuta ma znaczenie. Optymalizacja procesów, eliminacja strat oraz efektywne wykorzystanie czasu to podstawowe cele w każdej organizacji produkcyjnej. Choć 10 minut może wydawać się niewielką przerwą, w kontekście produkcji może oznaczać spore straty. Jak dokładnie wpływa na efektywność procesów? Odpowiedź na to pytanie zależy od perspektywy, z jakiej analizujemy te 10 minut.
1. Perspektywa pojedynczego procesu
W przypadku krótkich procesów produkcyjnych, gdzie czas cyklu wynosi tylko kilka minut, 10 minut może stanowić istotne opóźnienie. Dla przykładu:
Jeśli linia produkcyjna produkuje jeden wyrób na minutę, 10 minut przerwy oznacza 10 niewyprodukowanych jednostek.
W przypadku procesów wymagających sekwencyjnej współpracy, każda przerwa może zakłócić płynność produkcji i prowadzić do powstawania tzw. „wąskich gardeł”.
Wniosek: Z perspektywy pojedynczego procesu, nawet 10 minut to czas, który należy traktować poważnie, ponieważ może mieć wpływ na wydajność całego procesu produkcyjnego.
2. Perspektywa całej zmiany roboczej
Przeciętna zmiana robocza trwa 8 godzin (480 minut), więc 10 minut w tym kontekście to około 2% całego czasu pracy. Choć może się to wydawać niewielką ilością czasu, to:
Jeśli w ciągu dnia występują cztery takie przerwy po 10 minut, całkowita strata wynosi 40 minut, czyli 8% zmiany roboczej.
W skali tygodnia (5 dni roboczych) daje to aż 200 minut, czyli ponad 3 godziny niewykorzystanego czasu produkcyjnego.
Wniosek: Z perspektywy całej zmiany roboczej, nawet małe straty, takie jak 10 minut, mogą się kumulować i znacząco wpłynąć na wydajność produkcji.
3. Straty wynikające z 10 minut na różnych etapach produkcji
10 minut opóźnienia w produkcji może mieć różne skutki w zależności od etapu procesu:
Dział montażu: Brak dostarczenia surowców przez 10 minut może zatrzymać całą linię produkcyjną.
Transport wewnętrzny: Przestój w logistyce materiałowej może wpłynąć na synchronizację dostaw, co powoduje opóźnienia w całym procesie.
Awaria maszyny: Każde 10 minut przestoju wymaga dodatkowego wysiłku, aby nadrobić zaległości, a także może prowadzić do wzrostu kosztów produkcji.
Wniosek: Nawet krótka przerwa może odbić się na harmonogramie produkcji i powodować znaczące straty.
4. Czy zawsze trzeba minimalizować każdą minutę?
Warto zauważyć, że nie każda minuta przerwy oznacza stratę. W niektórych przypadkach, 10 minut może być korzystne:
Czas na analizę problemów: Krótkie zatrzymanie linii produkcyjnej może okazać się kluczowe, by zidentyfikować przyczyny problemów jakościowych i wdrożyć rozwiązania zapobiegawcze.
Przerwa na odpoczynek: Wprowadzenie planowanych przerw dla pracowników może zmniejszyć zmęczenie, poprawić morale zespołu oraz efektywność pracy.
Wniosek: Czasami warto poświęcić 10 minut na analizę, odpoczynek lub naprawę problemów, aby w dłuższej perspektywie uzyskać większe korzyści.
Jak skutecznie zarządzać czasem w produkcji?
Czas to najcenniejszy zasób, który mamy w produkcji. Nawet najmniejsze opóźnienia mogą prowadzić do dużych strat. Dlatego warto wdrożyć skuteczne strategie zarządzania czasem, które pozwolą zoptymalizować procesy i zwiększyć efektywność.
Kluczowe zasady zarządzania czasem:
Dokładna analiza procesów: Regularne monitorowanie każdego etapu produkcji pomoże zidentyfikować wąskie gardła i straty czasu.
Ustalanie priorytetów: Skup się na kluczowych zadaniach, które mają największy wpływ na wydajność.
Standaryzacja procesów: Wdrożenie standardów operacyjnych pozwala na eliminację nieefektywności i usprawnienie codziennej pracy.
Szkolenia i zaangażowanie zespołu: Wykształcenie kultury ciągłego doskonalenia wśród pracowników to klucz do sukcesu w zarządzaniu czasem.
Regularne audyty: Przeprowadzanie audytów procesów pozwala na bieżąco kontrolować czasochłonność i szybko identyfikować obszary do poprawy.
Podsumowanie
10 minut na produkcji to czas, który może być zarówno drobną chwilą, jak i bardzo znaczącą stratą. Kluczowe jest zrozumienie, w jakich miejscach te minuty są tracone oraz jakie mają konsekwencje dla całego procesu produkcyjnego. Dobrze przeprowadzona analiza czasu pracy, identyfikacja strat (np. przy użyciu metodologii Lean) oraz wdrożenie odpowiednich działań naprawczych pozwalają na efektywniejsze wykorzystanie czasu i zwiększenie produktywności.
Pamiętaj: to, czy 10 minut to dużo, zależy od tego, jak zarządzasz czasem na produkcji. Straty są nieuniknione, ale mogą być kontrolowane i minimalizowane.
Usługi audytowe oraz optymalizacyjne dla przedsiębiorstw produkcyjnych
Dane kontaktowe
krzysztof.kuczaj@aepp.pl
+48 796 375 845
© 2025. All rights reserved.